Supply chain challenges and labor shortages have become ubiquitous throughout the global manufacturing industry over the past few years. These issues aren’t going away any time soon, with an expected 2.1 million manufacturing jobs to go unfilled by 2030. Manufacturers struggle to fill their own positions, and the impact of reduced productivity reduces supply across the entire supply chain.
The Supply Chain Crisis and Manufacturing Staffing
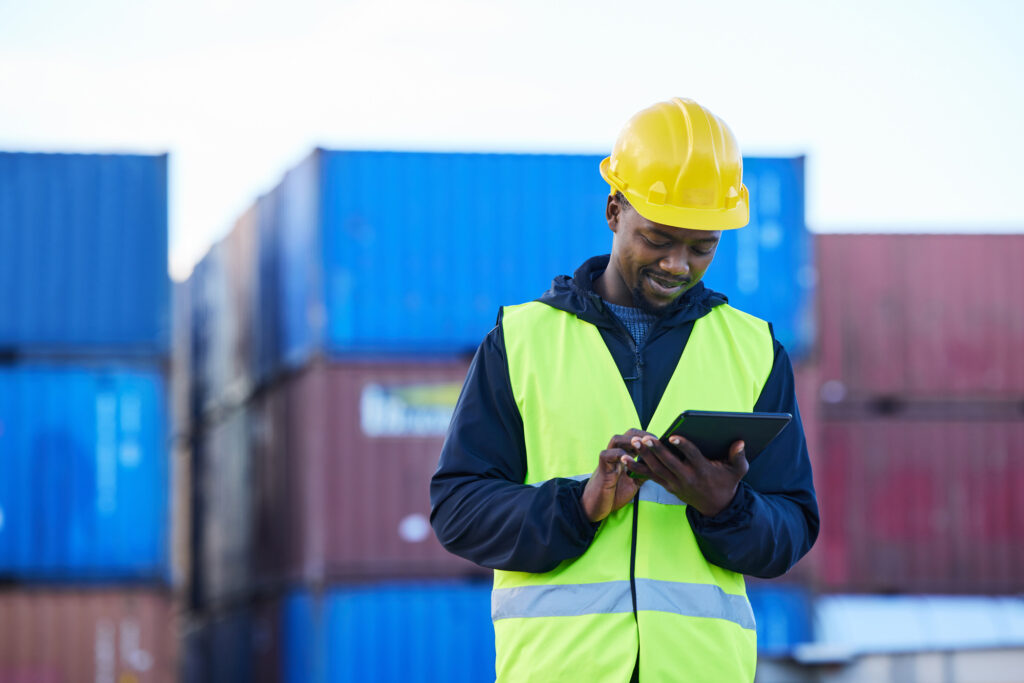
The COVID-19 pandemic sparked a major crisis in global supply chains during a time when many industries were already struggling. The early days of the pandemic saw US manufacturing alone lose 1.33 million jobs. The staggering impact that this had on productivity, combined with international freight and transport struggles, severely impacted global supply chains.
The effects of the shortage are still ongoing, with manufacturing companies worldwide reporting continued difficulties. Around 59% of manufacturers say that shipping delays are still impacting their supply chains, with 56% citing parts shortages and 53% stating talent shortages.
Many sectors have struggled to gain any recovery from these issues. The COVID-19 pandemic and the pressure it placed on supply chains revealed a variety of weaknesses in traditional practices that companies are still working to resolve.
Poor Structural Preparedness
In many cases, poor structural preparedness greatly increased the impact of the COVID-19 pandemic. Manufacturers and other organizations were not prepared for such a major disruption. Instead of building resilient supply chains that could continue to thrive under changing conditions, supply chains were fragile and featured too many single points of failure.
Sourcing strategies are one example where supply chains were not prepared. Having a single supplier for parts or raw materials placed too much reliance on that single relationship. Today, 81% of manufacturers say that they’ve taken steps to implement dual sourcing of raw materials in response to supply chain shortages.
Another key aspect of structural preparedness that failed under the pressure of the COVID-19 pandemic is inventory management. The just-in-time production philosophy had many manufacturers running as lean as possible, with minimal inventory to buffer any disruption. This trend has now reversed, with 80% of manufacturers taking steps to increase inventory along their supply chains.
Rapid Demand Shift
Manufacturing supply chains were unprepared for the disruption in the supply of labor, parts, and raw materials that the COVID-19 pandemic brought. However, that’s not the only way that the pandemic affected manufacturers. A shift in demand for specific products required specific manufacturing sectors to pivot and scale rapidly, and many were unable to do so effectively.
While the initial impact of the COVID-19 pandemic was a sharp drop in goods consumption, significant efforts to stimulate economies succeeded in spurring a rapid rise afterward. This meant that manufacturers were suddenly faced with higher demand than before the pandemic but were still faced with ongoing labor and supply chain shortages affecting their productivity.
Demand in many key areas was disproportionately affected. Semiconductor shortages were already a concern before the pandemic and reached a serious crisis point where demand significantly outpaced supply. Shipping and freight costs also increased dramatically under increased demand for both international and local shipping.
The Manufacturing Staffing Solution
The productivity of individual manufacturers has been greatly affected by challenges in manufacturing staffing. They cannot hire for manufacturing jobs and retain the skilled workers they need to meet demand.
Today, there are 693,000 job openings in the US manufacturing industry, adjusted for seasonal employment. This makes hiring incredibly competitive, and manufacturers also face higher turnover rates than the industry has typically experienced in the past.
These challenges are most acute when it comes to skilled tradespeople. Attracting and retaining trained and experienced workers within the industry is something that 54% of manufacturers say is among their top challenges today.
Better Staffing Solutions, Better Supply Chains
Among these ongoing challenges, many manufacturers are taking a closer look at their approach to staffing. Developing a resilient workforce in times of shifting demand and uncertainty is something that many manufacturers aren’t equipped to handle.
Taking on new job seekers to bolster a workforce for sudden boosts in demand simply isn’t viable. The process is too slow to meet demand effectively, and manufacturers can find themselves struggling to attract experienced manufacturing workers for short-term contracts. With demand so sporadic and unreliable, recruiting for skilled roles has become a challenge that many manufacturers can’t overcome.
Instead, turning to dedicated staffing solutions like Tradesmen International is becoming a more common approach. Through a manufacturing staffing agency, manufacturers can find skilled workers as needed with specific skill sets and disciplines. There’s no more struggling with recruitment or retention, but instead, a straightforward solution that lets you get the job done.
Finding the manufacturing employees you need when you need it can make all the difference in meeting demand and shifting workloads. You can ensure that your manufacturing operation fulfills its role in the supply chain and shows your value to customers, manufacturing clients, and partners.
The Tradesmen Staffing Difference
Working with manufacturing staffing agencies can solve a lot of problems for your manufacturing company, but only if you go with the right one. Tradesmen International focuses on innovative solutions in manufacturing and related industries, with a large pool of experienced workers and tradespeople covering all disciplines and specializations.
You can be sure to find the skilled workers you need when you need them. We carefully vet all of our teams to the highest standards of excellence. We can also work with you to create the perfect custom staffing solution based on the nature and timeline of your project. We’ll help you find the right number and type of skilled workers you need on your team to succeed.
We also make finding skilled support as easy as possible by handling all the details on our end. You don’t have to worry about paperwork, worker’s comp, benefits, or anything else involved in recruitment and onboarding.
Ease Manufacturing Staffing Issues With Tradesmen International
In the face of ongoing labor shortages in the most critical skilled manufacturing disciplines, you need a manufacturing staffing solution that delivers results today. Whether you’re expanding operations or need immediate support for essential roles, Tradesmen International provides skilled workers whenever you need them.